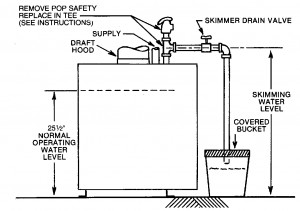
New steam boiler installations introduce chemicals, such as cutting oils, into the steam system. Mud and dirt build up in the system piping for years and often breaks loose during removal of the old boiler and installation of the new boiler. This often leads to foaming (priming) and surging of the boiler water. Surging and priming lead to low water cut-off shutting off the boiler and can also lead to boiler failure. Clean water is required to prevent this. Therefore new steam boiler installations require cleaning, this cleaning may require multiple return visits to the job.
A clean system and clean water are the goals. Even when you clean the boiler water in a new replacement boiler after operation scale, dirt and oils present in the system piping will be flushed back to the boiler.
Boiler and system cleaning
- Draining and flushing of the boiler will remove solid material and dissolved additives, however it does not remove oils, grease or other films that have lined the boiler and system piping.
- Chemical cleaners made specifically for steam boiler systems, such as Utility brand “Dry Stream”, help prevent priming and foaming surging, also loosen rust and mineral deposits and aid in cleaning of the boiler and system. Remember to flush all additives from the boiler and system after a week or two. Dry Steam is a product of Utility Manufacturing located in Westbury, NY. We have found Dry Steam to be an effective boiler cleaner.
- Dry Steam is a great cleaner and there are a couple of methods for “blowing-off” a Slant/Fin steam boiler.
- Galaxy GXH and GXHA boilers without tankless coils have a skimming trough built into the casting. This trough is located just below the normal water level. The double sided trough extends for 6 inches in the boiler casting, this gives 12 effective inches to skim the top layer (where the oils sit) of the water surface. Follow the detailed instructions within the Galaxy steam boiler installations instruction to take advantage of this unique feature.
- Boilers without a skimming trough.
- Turn off electrical power supply to boiler. Allow boiler to cool down and also allow pressure to reduce to zero before attempting removal of components. Check for pressure by testing pop safety valve. With no pressure in boiler install skimmer valve and skimming piping as shown in Figure B. Make sure the bucket used to catch skimming discharge if covered with a cloth to help prevent hot skimming discharge escaping the bucket and leading to a dangerous situation.
- Cautiously open the skimming valve, do not open the boiler drain valve. Slowly fill the boiler with water until water seeps into the bucket. Maintain this water level so you are just able to continue skimming. Fire the boiler and allow water the slowly skim and seep into the bucket. Empty the bucket frequently and continue skimming until water is clean and no oil can be seen floating on top of the water in the bucket. This process may have to be repeated until the system and system water are clean. On dirty systems this process may have to be repeated after a few days or weeks.
- When finished remove the skimming piping, remove tee below pop safety valve and install pop safety valve following the boiler’s installation manual.
- Never install a valve between the boiler and the pop safety valve. Install discharge piping on the pop safety valve following the boiler’s installation manual and local codes. Make sure all pipe connected to the pop safety valve is sized the same as the pipe connections to the valve. Never decrease the pipe size connected to the inlet and discharge sides of the pop safety. Never have a valve installed in the piping to or discharge side of the pop safety valve.
- Never add any type of chemical or cleaner to a steam boiler or steam system unless it is a product made specifically for steam systems. In a low pressure steam boiler water liquid expands around 1700 times when the water becomes low pressure steam. A lot of action goes on within a steam boiler so the boiler and system must be clean to produce quality dry steam into a steam heating system. Further, to ensure proper water level stability during steam boiler operation it is imperative the “near boiler piping” is installed exactly as detailed in our boilers’ installation instructions. During operation the pressure at the supply and return openings to the steam boiler must be equal, this is why you install the “equalizer” piping. Improper piping and cleaning of a steam boiler also leads to noisy banging (water hammer) in the system pipes. Steam velocity is fast and can exceed 40 miles per hour, this is one reason why “dry steam” is the only steam that should leave a steam boiler.
- We suggest you adjust the cut-out for the PA404A1009 Pressuretrol to a maximum of 2 P.S.I.G. with a 0.5 P.S.I.G. cut-in for normal residential boiler operation.
Cleaning and Service should only be done by Certified Contractors