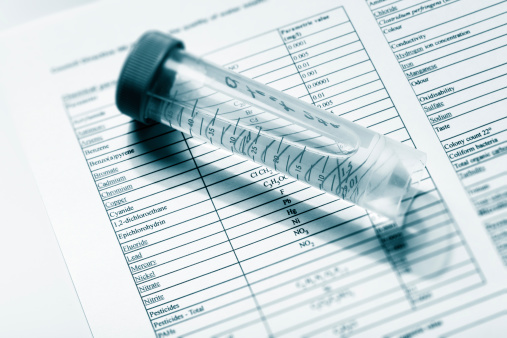
Water Quality is important to the proper operation of the boiler. The following information on water quality provided in this document must be followed. Damage caused by failure to follow these requirements may not be covered by the manufacturer’s warranty.
During installation and yearly maintenance, the water quality must be checked. Common water quality heat exchanger failures, are easily prevented when properly addressed.
Follow these system water best practices:
- Test system fill water and understand what you are putting into the system.
- Ensure that there is adequate air elimination in the system.
- Treat all boiler feed water as though it is hard water.
- Use chemical inhibitors on every job.
- Flush old and new systems with fresh clean water before commissioning a new boiler.
- Use magnetic dirt separators on systems containing large amounts of iron.
- Use Dirt Separators to remove debris from system water.
- Where possible, treat boiler feed water.
- Repair system leaks immediately to prevent oxygen (air) and untreated water from entering the system.
- Proper equipment must be used to test the water.
- Digital meters are highly recommended because they can be calibrated. The use of test strips is not recommended because they degrade over time and can be influenced by many factors.
System Cleaning
When a boiler is installed in a new system or an existing installation the system must be cleaned before the boiler installed. The system is required to be cleaned using a system cleaner from the list below or an equivalent hydronic system cleaner. Follow the instructions provided by the system cleaner manufacturer. The system should then be drained and thoroughly flushed with clean water to remove any residual cleaner. The system cleaner should never be run through the boiler.
- Noble Noburst Hydronic System Cleaner
- Fernox F3 Cleaner
- Rhomar Hydro-Solv 9100
- Sentinel X400
Air Elimination
A micro bubble air elimination device must be installed on every boiler installation. An air scoop is not an acceptable substitute for a micro bubble air elimination device and should not be used in a CHS installation. Below are a few examples of acceptable devices.
- Spirovent
- Taco 4900 series
- Caleffi Discal
Automatic feed valves should not be left open indefinitely. In the event of a minor leak in a system an automatic feed valve would continue to let into the system fresh water. Fresh water contains both oxygen and added minerals, one or both of these could lead to scaling and/or corrosion of the heat exchanger. It is therefore important that after a short period following installation of the boiler into a heating system that the automatic water feed valve be closed.
Dirt Removal
A dirt removal device should be installed in all systems. In older systems containing cast iron radiators/baseboard or large amount black iron or steel pipe a magnetic dirt separator must be installed.
Glycol, Snow Melt, and Oxygen Permeable Piping
When freeze protection is required only multi metal inhibited propylene glycol is allowed for use with the boiler A minimum of 20% and a maximum of 50% are allowed for use with boiler system. If the boiler is being used with a snow melt system that requires a concentration of glycol higher than 50% then a plate heat exchanger is required to be used to separate the snow melt system from the boiler water. In addition, if oxygen permeable piping (non-oxygen barrier tubing) is used in the system a plate heat exchanger is required to be used to separate it from the boiler water.
- Ethylene glycol is prohibited for use with the boiler, only inhibited propylene glycol is allowed for use with the boiler.
Water Treatment
When filling the system, the water is required to be tested. The following parameters in the table below outline what should be tested for and the corresponding ranges that are allowed. Water quality that does not fall with in the stated ranges below will void the warranty of the boiler. Proper testing equipment must be used such as digital meters.
- Never use Deionized (D.I), reverse osmosis, or distilled water to fill the system
- Never use petroleum based compounds in the system for cleaning or sealing
Inhibitors must be used for all installations in both new and existing heating systems. Follow the instructions provided by the inhibitor manufacturer when adding it to the system to ensure the correct concentration. A list of approved inhibitors is provided below.
- Rhomar Pro-tek 922
- Sentinel X100
- Fernox Protector F1
It is important to understand what each of the parameters of water quality mean, and how a deviation from the recommended range will cause damage to your system. The following explains in more detail each of the above parameters:
Corrosion Inhibitors
Corrosion in systems can come in many forms. The most common form known to most people is corrosion that is caused by oxygen in the water. This corrosion is called oxidative corrosion. Other types of corrosion include galvanic corrosion, caustic corrosion and acidic corrosion. To combat corrosion, many different methods are used such as control of pH (see pH section), use of chemical corrosion inhibitors and effective monitoring and control.
There are many chemical corrosion inhibitors available on the market today. Molybdate corrosion inhibitors are film forming inhibitors and protect against all forms of corrosion. Molybdate is recommended because it is required at a lower concentration, it is less toxic and does not promote the growth of bacteria. The Molybdate works by converting “red rust” into the same passive layer of magnetite. The concentration of Molybdate inhibitor should be between 100-150ppm (parts per million). Concentrations above 150ppm Molybdate are not a concern.
Doubling the Molybdate corrosion inhibitor concentration to approximately 300ppm, in conjunction with a side stream filter, is an effective post-operational cleaner. The Molybdate will remove oils and minor debris from the system and will collect it in the filter. Without the filter, the cleaning properties of this method will not be effective.
pH
A pH measurement is a logarithmic determination of the hydrogen concentration. The lower the pH reading the more acidic the solution; the higher the pH the more basic the solution. The pH scale ranges from 1 to 14 with a pH of 7 being neutral.
The pH of a system has a huge effect on the life of the system. Variations in pH can indicate a variety of problems and cause damage to the system components. The ideal pH is between 7.0 and 9 pH units. Systems should be maintained in this range because a low pH will promote steel corrosion and a high pH will promote copper and brass corrosion. A high pH will also cause the precipitation of iron from the water. Buffers in the inhibitors can help maintain the proper pH range. A drop in pH can indicate a variety of problems. First, a bacterial infection can produce acidic by-products which will drop the pH. This can be combated by the addition of a biocide (see Bacteria/Mold section). Also, as glycol degrades, it produces acidic by-products that can drop the pH. The pH of the system can be maintained by monitoring the pH with a pH meter. Check with the glycol manufacturer for the correct pH range for the product you are using.
Conductivity
Conductivity is an indirect measurement of Total Dissolved Solids (TDS) in the water (TDS = 0.62 x Conductivity). Conductivity is a test of how easily the water can conduct an electrical current. The more dissolved solids in the solution the higher the conductivity. Domestic tap water has a conductivity of about 300μS/cm (with variances depending on your particular region). Conductivity can also be used as a secondary indication of the amount of chemicals in the water. As an example, the concentration of nitrite in a solution should be approximately 1/3 the conductivity reading.
The conductivity in a closed loop hydronic heating systems should be between 100 and 300μS/cm depending on which additives are in the water. The addition of glycol, nitrite, and even soft water, will have an effect on the conductivity reading. Conductivity above 300μS/cm indicates a high level of dissolved solids and the water becomes physically aggressive and will breakdown O-rings. In systems where the conductivity is approaching or above 300μS/cm the system should be flushed and refilled with fresh water, glycol (if required) and corrosion inhibitors.
Hardness
Water hardness is a term that describes the amount of calcium and magnesium bicarbonate in the water. These ions have the ability to precipitate out of water as calcium carbonate and magnesium carbonate when the water is heated. This can be seen on a daily basis if you have a white/yellow scale on your kitchen sink faucet. These precipitated particles have the ability to cause leaks by getting behind O-rings and allowing water to escape. Also, the precipitation of these substances onto mechanical parts can cause improper functioning of the part.
Hardness is usually measured in “Grains of Hardness” (grains/USG) or in parts per million of CaCO3. Converting between the two units is simple using the ratio of 1 grain/USG = 17.1ppm. We will be using ppm in our discussion.
The ‘old school’ of water quality recommended the use of soft water in closed loop systems. This was because it was thought that the precipitation of CaCO3 needed to be controlled. The new school of thought is that hard water can be used in closed loop systems. The reason for the change is that softened water has had the natural mineral balance disturbed. The disturbed water will then try to re-balance itself by leaching the required minerals from the metals back into the water; this leaching of minerals will cause a higher rate of corrosion. To help combat the precipitation of CaCO3 without softening the water, dispersants are included in the corrosion inhibitor mixtures that keep the CaCO3 in the water. Water hardness will vary depending on the region you live. For example, water in Tampa Florida has a hardness of above 15 gpg where as Boston Massachusetts has a hardness of about 1 gpg.
Water with a hardness above 11.7 gpg can lead to scale build up, even with the use of corrosion inhibitors, and should not be used.
Glycol Freeze Protection
Propylene glycol is used to prevent the freezing of systems that are exposed to low temperature environments, such as snowmelt systems. If glycol is required in a system, it is recommended that the concentration of glycol be above 20% and no more than 50%. Below 20%, glycol becomes a nutrient for the growth of bacteria, which can infect the system. Once a bacterial infection gets into a system, it is very difficult to remove. A glycol concentration above 50% creates a high viscosity fluid and will cause damage to a variety of components and moving parts. Also, high glycol concentration causes the system to lose some heat transfer ability and decrease the system efficiency; this decrease is dramatic in mixtures that are above 50%. Propylene glycol can have a life up to 9 years, but follow the manufacturers instructions for testing the glycol to ensure it is still effective.
Addition of glycol to a system will cause a drop in the pH (see pH section). Buffers are usually mixed with the glycol to combat a drop in pH. When glycol breaks down it causes acidic products to be formed which can also lower the pH. Inhibited glycol will typically have a pH of 8-9 when mixed at a 30-50% concentration, check with the glycol manufacturer for the proper pH level. The use of UV water filters in glycol systems is not recommended because UV radiation will degrade glycol.
Bacteria and Mold
There are different types of bacteria that can infect a system. Bacterial infections are rare but appear occasionally. As previously mentioned, bacteria can thrive in a glycol environment in concentrations below 20%. This is because at a low concentration, the glycol is no longer toxic to the bacteria and the bacteria can feed off of it. The bacteria can leave a slime residue that interferes with proper operation of the system (the excrement of the bacteria can be highly corrosive, often indicated by “pin-hole” leaks in the heating system).
Microbiological organisms can enter a system through the make-up water. A certain amount can also enter the water through air dissolving into the water. Testing for bacterial and mold infections can be done using agar dip slides. If an infection is found, the easiest way to remove the organisms is to add dispersants and biocide to the system. Both products can be purchased through any pool supply store.
The following scale conditions may occur when the recommended guidelines are not followed:
Scaling in Hot Water Boilers
Scale is a general term used to describe mineral deposits formed from dissolved minerals in water. These deposits restrict flow in the boiler and heating system, reduce efficiency and damage system components. Scale formation in hydronic heating systems has three main causes, use of hard water, aerated hydronic systems, and poorly maintained heating systems. Three common types of scale found in boilers are, lime scale, magnetite, and hematite.
Lime scale is a chalky off-white material commonly found in kettles, shower heads and boilers. This type of scale is formed when naturally occurring calcium carbonate, magnesium hydroxide and calcium sulphite, found in most ground water supplies, is heated and then precipitates onto the boiler or system piping. Tests for water hardness measure the level of calcium carbonate and magnesium hydroxide in a water sample. Hardness is typically measured in grains per gallon (gpg), parts per million (ppm), or milligrams per liter (mg/L).
Magnetite scale is a hard, brownish-black material that is found in closed loop heating systems. Magnetite is formed when iron corrodes in a closed loop water system and the dissolved oxygen in the water is limited. It is normal for some magnetite to occur in heating systems where iron is present and corrosion inhibitors work by creating a passive layer of magnetite on iron components. The initial water fill will always contain some dissolved oxygen which will react with exposed iron and create magnetite. In Closed loop systems, there is a limited amount of dissolved oxygen available and magnetite formation will be negligible. Free magnetite in heating systems can be reduced with the use of magnetic filters. Magnetite will not be detected by a harness test but will evidence itself in total dissolved solids, conductivity, or iron specific tests.
Hematite or rust scale is reddish-brown in color and is found wherever unprotected iron is exposed to moisture and oxygen. Rust will form in heating systems when there is too much oxygen present. Oxygen is introduced in heating systems from inadequate air elimination, non-oxygen barrier components, and excessive make up water. Rust formation in a heating system requires immediate action to prevent system damage. Systems with evidence of hematite formations must be thoroughly cleaned and the water in these systems should be monitored closely for the several months to ensure that pockets of rust do not come loose and contaminate the fresh system water. Hematite is nonmagnetic and will not be picked up with magnetic filters.